Bulkhead Construction and Repair: A Charleston Waterfront Essential
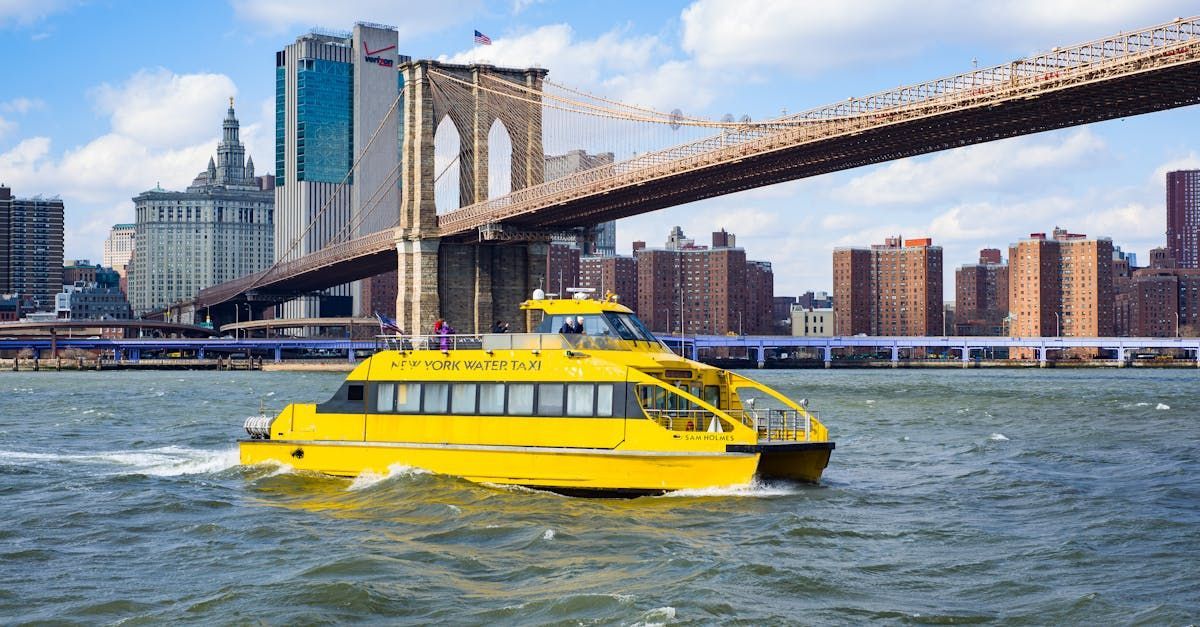
Bulkhead construction and repair are critical for protecting Charleston's waterfront properties from erosion and flooding. These structures play a vital role in maintaining the integrity of coastal land and safeguarding homes and businesses along the city's many waterways. Let's explore the key aspects of bulkhead construction and repair in the context of Charleston's unique coastal environment.
Key takeaways:
- Bulkheads are essential structures for protecting Charleston's waterfront properties
- Regular maintenance and timely repairs are crucial for bulkhead longevity
- Charleston's tidal patterns and soil conditions impact bulkhead design and construction
- Proper material selection is vital for durability in the local marine environment
- Permitting and environmental regulations are important considerations for bulkhead projects
- Professional expertise is necessary for successful bulkhead construction and repair
Understanding Bulkheads in Charleston's Coastal Landscape
Bulkheads are vertical structures designed to hold back soil and water, providing a barrier between land and water. In Charleston, these structures are particularly important due to the city's low-lying coastal areas and numerous tidal creeks and rivers. Bulkheads help prevent erosion, stabilize shorelines, and protect properties from storm surges and flooding.
The role of bulkheads in Charleston's waterfront protection
Charleston's waterfront is a mix of historic properties, modern developments, and natural habitats. Bulkheads serve as a first line of defense against the constant forces of water and weather. They help maintain property boundaries, create usable waterfront space, and protect infrastructure from the damaging effects of erosion and flooding.
Charleston's unique coastal challenges
The Lowcountry's soft, sandy soils and frequent tidal fluctuations present unique challenges for bulkhead construction and maintenance. The area's subtropical climate, with its hot summers and occasional hurricanes, also contributes to the wear and tear on these structures. Understanding these local factors is crucial for designing and building effective bulkheads that can withstand Charleston's coastal conditions.
Materials Used in Charleston Bulkhead Construction
Choosing the right materials for bulkhead construction is crucial for longevity and performance in Charleston's marine environment. Several options are available, each with its advantages and considerations.
Wood bulkheads: A traditional choice
Wood has been a popular material for bulkheads in Charleston for many years. It's relatively affordable and easy to work with, making it a common choice for residential properties. However, wood is susceptible to rot, marine borer damage, and weathering, which can shorten its lifespan in the harsh coastal environment.
Concrete bulkheads: Durability for the long term
Concrete bulkheads offer excellent durability and longevity, making them a popular choice for commercial properties and areas with heavy wave action. They can withstand the corrosive effects of saltwater and provide a strong barrier against erosion. However, concrete bulkheads are more expensive to install and may require specialized equipment.
Steel bulkheads: Strength and versatility
Steel bulkheads are known for their strength and ability to be driven deep into the ground, providing excellent stability. They're often used in areas with poor soil conditions or where space is limited. However, steel can corrode in saltwater environments, so proper coating and maintenance are essential.
Vinyl and composite materials: Modern alternatives
Vinyl and composite materials are gaining popularity for bulkhead construction in Charleston. These materials offer excellent resistance to rot, corrosion, and marine borers. They're also low-maintenance and can be designed to mimic the appearance of traditional wood bulkheads. While initially more expensive, their long-term durability can make them a cost-effective choice.
The Bulkhead Construction Process in Charleston
Building a bulkhead in Charleston requires careful planning, design, and execution. The process involves several steps, each crucial for creating a sturdy and effective structure.
Site assessment and design
The first step in bulkhead construction is a thorough site assessment. This involves analyzing the soil conditions, water depth, tidal patterns, and potential environmental impacts. Engineers use this information to design a bulkhead that meets the specific needs of the site and complies with local regulations.
Permitting and environmental considerations
Before construction can begin, property owners must obtain the necessary permits from local and state agencies. In Charleston, this often involves working with the South Carolina Department of Health and Environmental Control (DHEC) and the U.S. Army Corps of Engineers. Environmental impact assessments may be required to ensure the project doesn't harm local ecosystems or wildlife habitats.
Excavation and site preparation
Once permits are secured, the construction site is prepared. This may involve clearing vegetation, excavating the shoreline, and creating a level surface for the bulkhead. In some cases, existing structures may need to be removed or modified.
Installation of the bulkhead
The actual installation process varies depending on the chosen materials and design. For example, wooden bulkheads typically involve driving pilings into the ground and attaching horizontal planks. Concrete bulkheads may require forming and pouring on-site or installing precast sections. Steel sheet piling is often driven into the ground using specialized equipment.
Backfilling and finishing
After the main structure is in place, the area behind the bulkhead is backfilled with appropriate materials to provide additional support and create a level surface. Drainage systems may be installed to prevent water buildup behind the bulkhead. Finally, the area is graded and landscaped to complete the project.
Common Bulkhead Repair Issues in Charleston
Even well-constructed bulkheads require maintenance and occasional repairs. Several issues are common in Charleston's coastal environment.
Erosion and scour
The constant action of waves and tides can erode the soil at the base of a bulkhead, leading to instability. This process, known as scour, can undermine the structure and cause it to fail if not addressed promptly.
Rotting and marine borer damage
Wooden bulkheads are particularly susceptible to rot and damage from marine borers, which are prevalent in Charleston's waters. Regular inspections can help catch these issues early before they compromise the structure's integrity.
Corrosion of metal components
Steel bulkheads and the metal fasteners used in wooden structures can corrode in the saltwater environment. This can weaken the bulkhead and lead to structural failures if not addressed.
Cracking and spalling in concrete bulkheads
Concrete bulkheads may develop cracks or spalling (flaking of the surface) over time due to weathering, freeze-thaw cycles, or settlement. These issues can allow water to penetrate the structure, leading to further damage if not repaired.
Tie-back system failures
Many bulkheads use tie-back systems to provide additional support. These systems can fail due to corrosion, soil movement, or improper installation, leading to bulkhead instability.
Bulkhead Repair Techniques for Charleston Properties
When issues arise, prompt and effective repairs are essential to maintain the integrity of the bulkhead and protect the property.
Patching and sealing
Minor cracks and holes in concrete or wood bulkheads can often be repaired by patching and sealing. This helps prevent water infiltration and further damage.
Reinforcement and stabilization
For bulkheads showing signs of instability, reinforcement techniques such as installing additional tie-backs or sheet piling can help restore structural integrity.
Replacement of damaged components
In some cases, individual components of the bulkhead may need to be replaced. This could involve replacing rotted wooden planks, corroded steel sheets, or damaged concrete sections.
Scour protection
To address erosion and scour issues, various techniques can be employed, such as installing rip-rap (large stones) at the base of the bulkhead or using geotextile fabrics to prevent soil erosion.
Cathodic protection
For steel bulkheads, cathodic protection systems can be installed to prevent corrosion by using sacrificial anodes or impressed current systems.
Maintaining Charleston Bulkheads for Longevity
Regular maintenance is key to extending the life of a bulkhead and preventing costly repairs.
Regular inspections
Conducting regular visual inspections can help identify potential issues before they become serious problems. Look for signs of erosion, cracks, rot, or other damage.
Cleaning and debris removal
Keeping the bulkhead clean and free of debris can prevent damage and allow for easier inspections. This is particularly important after storms or high tides.
Preservative treatments
For wooden bulkheads, applying preservative treatments can help protect against rot and marine borer damage. This should be done according to manufacturer recommendations and environmental regulations.
Addressing drainage issues
Ensuring proper drainage behind the bulkhead can prevent soil erosion and reduce pressure on the structure. This may involve maintaining or improving existing drainage systems.
Monitoring water levels and erosion
Keeping an eye on water levels and any changes in erosion patterns can help property owners anticipate potential issues and take proactive measures.
Environmental Considerations for Charleston Bulkhead Projects
Bulkhead construction and repair in Charleston must take into account the area's sensitive coastal ecosystems.
Protecting marine habitats
Care must be taken to minimize the impact on marine habitats during construction and repair. This may involve using environmentally friendly materials or incorporating design features that promote marine life.
Managing stormwater runoff
Proper stormwater management is crucial to prevent pollutants from entering waterways. This may involve incorporating filtration systems or creating buffer zones.
Preserving natural shorelines
Where possible, incorporating natural shoreline elements into bulkhead design can help maintain ecological balance and provide habitat for local wildlife.
Compliance with environmental regulations
All bulkhead projects must comply with local, state, and federal environmental regulations. This may include obtaining permits and conducting environmental impact assessments.
Choosing a Bulkhead Contractor in Charleston
Selecting the right contractor is crucial for successful bulkhead construction and repair projects.
Verifying licenses and insurance
Ensure that any contractor you consider is properly licensed and insured to work in Charleston. This protects both you and the contractor in case of accidents or issues during the project.
Checking references and past projects
Ask for references and examples of past bulkhead projects in the Charleston area. This can give you a sense of the contractor's experience and the quality of their work.
Understanding the bidding process
Get detailed bids from multiple contractors and make sure you understand what is included in each bid. Be wary of bids that seem unusually low, as they may not account for all necessary work or materials.
Evaluating experience with local conditions
Choose a contractor who has experience working in Charleston's specific coastal conditions and is familiar with local regulations and permitting processes.
The Future of Bulkhead Technology in Charleston
As Charleston faces increasing challenges from sea-level rise and more frequent storms, bulkhead technology continues to evolve.
Innovative materials
New materials are being developed that offer improved durability and environmental performance. These may include advanced composites or bio-based materials that are more resistant to corrosion and marine growth.
Smart monitoring systems
Emerging technologies like sensors and remote monitoring systems can help property owners and managers track the condition of their bulkheads in real time, allowing for more proactive maintenance and repair.
Nature-based solutions
There's growing interest in incorporating natural elements into bulkhead design, such as living shorelines that combine traditional structures with native vegetation and natural habitats.
Adaptive design strategies
As sea levels rise, bulkhead designs may need to adapt. This could involve creating structures that can be easily raised or modified over time to accommodate changing water levels.
Protecting Charleston's Waterfront Legacy
Bulkhead construction and repair are essential components of preserving Charleston's unique coastal character and protecting its waterfront properties. By understanding the importance of these structures, the challenges they face, and the best practices for their construction and maintenance, property owners can play a crucial role in safeguarding the city's shorelines for future generations.
Whether you're considering a new bulkhead project or need to repair an existing structure, it's important to work with experienced professionals who understand Charleston's specific coastal conditions and regulatory environment. With proper planning, construction, and maintenance, bulkheads can continue to protect Charleston's waterfront properties while preserving the natural beauty and ecological balance of the Lowcountry's coastal areas. For more information, you can visit our website or contact us.
- Material Advantages Disadvantages Typical Lifespan in Charleston Wood
- Affordable
- Easy to install
- Natural appearance
- Susceptible to rot and marine borers
- Requires frequent maintenance
- Shorter lifespan 15-20 years with proper maintenance Concrete
- Highly durable
- Resistant to saltwater
- Low maintenance
- Expensive to install
- May require heavy equipment
- Can be visually imposing 30-50 years or more Steel
- Strong and versatile
- Can be driven deep for stability
- Suitable for poor soil conditions
- Prone to corrosion in saltwater
- Requires protective coatings
- Can be noisy to install 25-40 years with proper corrosion protection Vinyl/Composite
- Resistant to rot and corrosion
- Low maintenance
- Can mimic the wood appearance
- Higher initial cost
- May lack structural strength of other materials
- Limited repair options 30-50 years Bulkhead Issue Potential Causes Repair Techniques Prevention Strategies Erosion and Scour
- Wave action
- Tidal fluctuations
- Poor drainage
- Install rip-rap
- Use geotextile fabrics
- Improve drainage
- Regular inspections
- Maintain proper grading
- Install scour aprons Rotting (Wood)
- Moisture exposure
- Marine borers
- Lack of preservative treatment
- Replace damaged sections
- Apply preservatives
- Install protective barriers
- Use treated lumber
- Regular preservative application
- Maintain proper drainage Corrosion (Steel)
- Saltwater exposure
- Inadequate protective coatings
- Stray electrical currents
- Apply protective coatings
- Install cathodic protection
- Replace severely corroded sections
- Use corrosion-resistant alloys
- Regular coating inspections
- Proper electrical grounding Cracking (Concrete)
- Settlement
- Freeze-thaw cycles
- Poor mix design
- Epoxy injection
- Patching
- Structural reinforcement
- Proper mix design
- Adequate reinforcement
- Control joint installation Common signs of bulkhead deterioration in Charleston:
- Visible cracks or holes in the structure
- Leaning or bowing of the bulkhead wall
- Erosion or sinkholes behind the bulkhead
- Exposed tie-backs or anchors
- Vegetation growing in joints or cracks
- Rust stains on concrete or wood surfaces
- Soft or spongey wood in wooden bulkheads
- Separation between bulkhead sections
- Accumulation of sediment in front of the bulkhead
- Changes in the water level or shoreline position