Expert Storm Damage Dock Repair: Restore & Protect
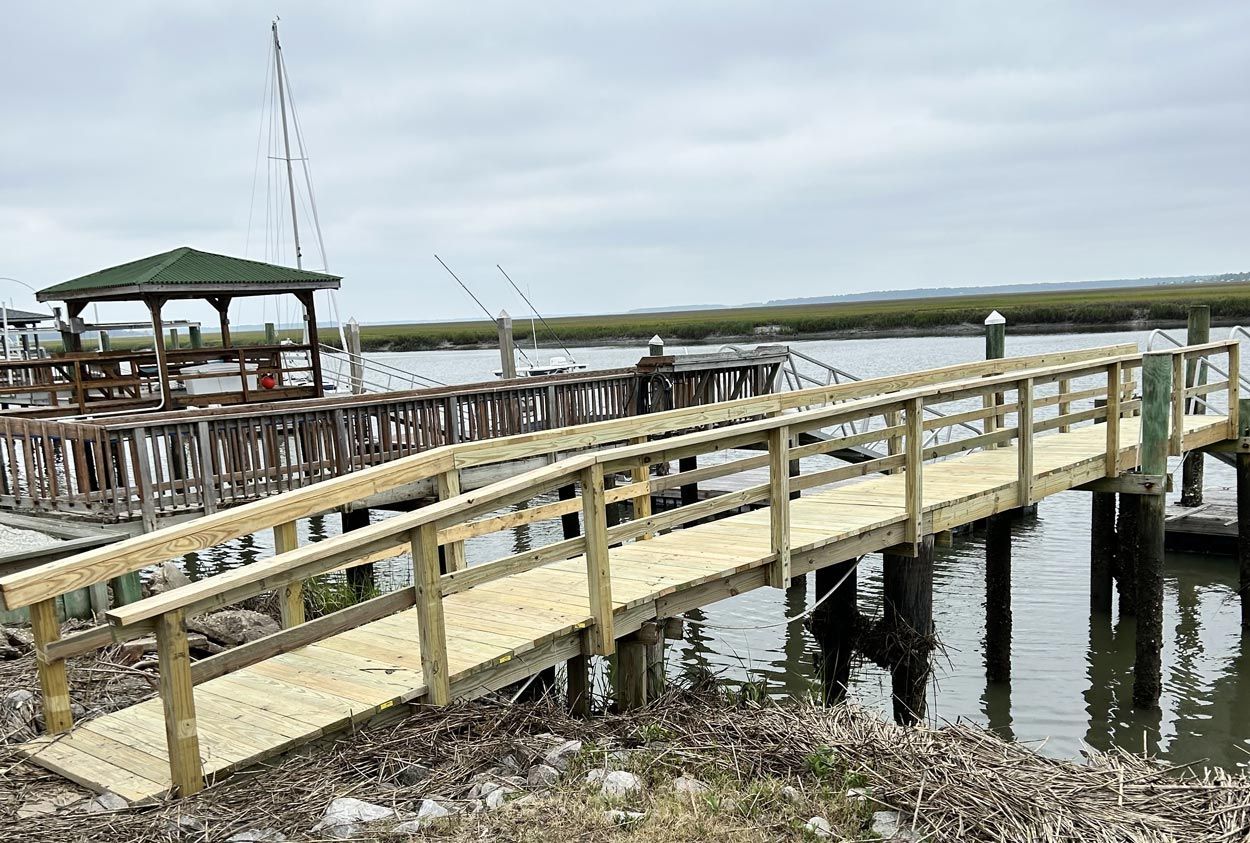
Effective Strategies for Storm Damage Dock Repair
Storm damage dock repair requires immediate and effective action to restore the functionality and aesthetic appeal of your waterfront property. Severe weather conditions can wreak havoc on docks, causing structural damages that, if left unattended, can escalate into more significant issues. Comprehensive solutions to address storm damage dock repair, ensuring your dock remains safe and durable.
Key Takeaway
- Immediate Assessment: Conduct a thorough assessment of the dock to identify visible and hidden damages.
- Expert Inspection: Engage professionals for a detailed inspection to uncover structural vulnerabilities.
- Material Quality: Use high-quality, weather-resistant materials for repair work.
- Preventative Measures: Implement preventive strategies to safeguard your dock against future storm damage.
- Regular Maintenance: Schedule routine maintenance checks to prolong the lifecycle of your dock.
Understanding the Impact of Storm Damage on Docks
Storms can cause a range of damages to docks, from minor cosmetic issues to severe structural problems. High winds, heavy rain, and flooding can result in:
- Loose or missing boards
- Cracked or splintered wood
- Corroded or weakened fasteners
- Compromised pilings or supports
- Damaged floating components
Addressing these issues promptly is crucial to prevent further deterioration and ensure safety.
Initial Assessment and Immediate Actions
When a storm subsides, it's vital to assess your dock for damages. Walk the entire length of your dock, checking for loose boards, visible cracks, and other signs of damage. Pay close attention to the following:
- Decking: Look for any broken or missing boards.
- Supports: Check pilings and supports for signs of shifting or weakening.
- Hardware: Inspect bolts, screws, and other hardware for corrosion or damage.
Consider taking photographs of the damages for reference and insurance purposes.
Common Storm-Induced Dock Damages
Damage Type Symptoms Immediate Action
- Loose/Missing Boards Boards that are dislodged or absent - Reinforce or replace immediately
- Cracked Wood Splintered or visibly cracked wood - Replace damaged sections
- Corroded Fasteners Rusty or weakened bolts, screws, and nails - Replace with weather-resistant hardware
- Compromised Pilings Shifts, cracks, or visible wear on pilings - Consult a professional for repair
- Floating Component Damage Broken or damaged floatation devices - Replace or repair floatation units
The Role of Professional Inspections
Engaging a professional for a detailed inspection is essential. Experts can identify hidden structural issues that may not be visible to the untrained eye. Professional inspectors will:
- Assess the overall structural integrity.
- Use specialized tools to detect internal damages.
- Provide a comprehensive report with recommended repairs.
Prioritizing Quality Materials for Repairs
Using high-quality, weather-resistant materials ensures longevity and durability. Common materials include:
- Pressure-treated wood: Resistant to rot and insect damage.
- Composite decking: Low maintenance and highly durable.
- Stainless steel fasteners: Offers resistance to corrosion and rust.
- Concrete pilings: Provides robust support and longevity.
Ensuring that these materials are used in repairs will contribute to a more resilient dock structure.
Recommended Materials for Storm Damage Dock Repair
Material Benefits Common Uses
- Pressure-Treated Wood Rot and insect resistance Decking, supports
- Composite Decking Low maintenance, durable Decking
- Stainless Steel Rust and corrosion resistance Fasteners, hardware
- Concrete Pilings Robust and long-lasting Structural support
Implementing Preventative Measures
To protect your dock from future storm damage, implement these preventive strategies:
- Install Bumpers: Bumpers absorb impacts from boats and debris.
- Secure Loose Items: Remove or secure loose items before a storm.
- Ensure Proper Drainage: Effective drainage prevents water logging and wood rot.
- Reinforce Structural Components: Regularly reinforce or replace weak components.
- Utilize Floating Docks: Floating docks can move with water levels, reducing stress on structural elements.
Routine Maintenance for Dock Longevity
Regular maintenance is key to extending the lifespan of your dock. Schedule routine checks every six months to:
- Inspect for new damages or wear and tear.
- Tighten loose fasteners and replace corroded ones.
- Clean the dock to prevent mold and mildew growth.
- Apply sealants or protective coatings as needed.
Routine Maintenance Checklist
- Inspect decking for cracks and loose boards.
- Check the condition of the pilings and supports.
- Tighten or replace damaged hardware.
- Clean off debris, mold, and mildew.
- Apply protective sealants.
Real-Life Experience: The Value of Timely Repairs
One of our clients in Charleston experienced significant storm damage to their dock, including loose boards and cracked supports. Immediate action was taken by our team, conducting a thorough inspection and using only quality materials for repairs. The client was impressed with the swift response and the durability of the repaired dock, emphasizing the importance of professionalism and quality in storm damage dock repair.
Conclusion
Timely storm damage dock repair is critical in maintaining the structural integrity and aesthetic appeal of your waterfront property. By conducting immediate assessments, engaging professionals, using quality materials, implementing preventive measures, and scheduling regular maintenance, you can ensure your dock withstands adverse weather conditions and continues to provide safe, reliable service.
For all your storm damage dock repair needs, trust the experts at Baker Marine Contracting. Contact us today to schedule a free consultation and get a free estimate for your dock repair project.
Enhance your dock's resilience and functionality with Baker Marine Contracting's expert storm damage repair services.