Ultimate Guide: Pressure-Treated Lumber for Docks
Pressure-treated lumber is the go-to material for building docks in Charleston, South Carolina. Its durability and resistance to moisture make it ideal for waterfront structures. This guide will cover everything you need to know about using pressure-treated wood for your Charleston dock project.
Key Takeaways
- Pressure-treated lumber is essential for dock construction in Charleston's humid climate
- Marine-grade treatment offers the best protection against saltwater and moisture
- Southern yellow pine is the most common wood species used for treated dock lumber
- Proper maintenance can extend the life of pressure-treated dock wood by 20-30 years
- Local building codes in Charleston require specific grades of pressure-treated lumber for marine use
- Environmental considerations are important when choosing and using treated wood near water
Why Pressure-treated Lumber is Crucial for Charleston Docks
Charleston's coastal environment demands materials that can withstand constant exposure to moisture, salt, and marine organisms. Pressure-treated lumber meets these challenges head-on. The treatment process involves forcing preservative chemicals deep into the wood fibers, creating a barrier against decay and insect infestation.
The science behind pressure treatment
The pressure treatment process uses a combination of vacuum and high pressure to force preservatives into the wood's cellular structure. This results in protection that goes far beyond surface-level coatings. For dock builders in Charleston, this means a structure that can stand up to the harsh coastal conditions for decades.
Benefits of pressure-treated wood for Charleston docks
Choosing pressure-treated lumber for your Charleston dock offers several advantages:
- Resistance to rot and decay: The preservatives protect against fungal growth and wood-destroying organisms.
- Insect repellent: Treated wood deters termites and other wood-boring insects common in the Lowcountry.
- Longevity: Properly maintained pressure-treated docks can last 20-30 years in Charleston's climate.
- Cost-effective: Compared to alternatives like composite materials, pressure-treated wood offers good value.
- Strength: The treatment process doesn't compromise the wood's structural integrity.
Selecting the Right Grade of Pressure-Treated Lumber
Not all pressure-treated lumber is created equal, especially when it comes to marine applications in Charleston. The American Wood Protection Association (AWPA) sets standards for treated wood based on its intended use.
Understanding AWPA use categories
For dock construction in Charleston, you'll want to focus on two main categories:
- UC4A: For wood used in freshwater applications
- UC4B: For wood exposed to saltwater splash in coastal areas
Given Charleston's location on the Atlantic coast, most dock projects will require UC4B-rated lumber to withstand saltwater exposure.
Best wood species for Charleston docks
While several wood species can be pressure-treated, southern yellow pine is the most common choice for dock construction in Charleston. It's readily available, takes treatment well, and offers good strength properties.
Critical Factors in Pressure-Treated Lumber Selection
When choosing pressure-treated lumber for your Charleston dock, consider these important factors:
Retention levels
Retention refers to the amount of preservative in the wood. For marine use in Charleston, look for lumber with higher retention levels, typically measured in pounds of preservative per cubic foot of wood (pcf).
Types of preservatives
Different preservatives offer varying levels of protection. For saltwater exposure in Charleston, copper-based preservatives like ACQ (Alkaline Copper Quaternary) or CA (Copper Azole) are most effective.
Moisture content
Freshly treated lumber can have a high moisture content. Allow the wood to dry properly before installation to prevent warping and splitting in Charleston's humid climate.
Installation Tips for Pressure-Treated Dock Lumber
Proper installation is key to maximizing the lifespan of your pressure-treated dock in Charleston.
Fastener selection
Use stainless steel or hot-dipped galvanized fasteners to prevent corrosion. The salt air in Charleston can quickly deteriorate standard fasteners.
Cutting and drilling
When cutting or drilling pressure-treated lumber, always apply a preservative to the exposed areas. This helps maintain the wood's integrity in Charleston's moist environment.
Spacing and ventilation
Allow for proper spacing between deck boards to promote air circulation and prevent water pooling, which is crucial in Charleston's rainy seasons.
Maintaining Your Pressure-Treated Dock
Regular maintenance will extend the life of your pressure-treated dock in Charleston's challenging climate.
Annual inspections
Check for signs of wear, loose boards, or protruding fasteners each year, especially after hurricane season.
Cleaning
Regularly clean your dock to remove salt buildup, algae, and other marine growth common in Charleston waters.
Sealing and staining
Apply a water-repellent sealer or stain every few years to provide additional protection against moisture and UV damage.
Environmental Considerations
While pressure-treated lumber is effective for dock construction, it's important to consider its environmental impact, especially in Charleston's sensitive coastal ecosystem.
Eco-friendly alternatives
Some Charleston dock builders are exploring more environmentally friendly options like acetylated wood or naturally rot-resistant species like black locust.
Proper disposal
When replacing old pressure-treated lumber, follow Charleston's guidelines for proper disposal to prevent contamination of local waterways.
Local Regulations and Permits
Before starting your dock project in Charleston, familiarize yourself with local building codes and permit requirements.
Charleston County building codes
Charleston County has specific requirements for dock construction, including the use of marine-grade pressure-treated lumber.
Permitting process
You'll need to obtain permits from both local and state agencies before building a dock in Charleston waters.
Cost Considerations for Charleston Dock Projects
Building a dock with pressure-treated lumber in Charleston involves several cost factors:
Material costs
Pressure-treated lumber prices can vary based on treatment level and current market conditions. In Charleston, expect to pay a premium for marine-grade lumber.
Labor costs
Professional dock builders in Charleston typically charge by the square foot or linear foot for installation.
Long-term value
While initial costs may be higher for quality pressure-treated lumber, the long-term durability in Charleston's climate often makes it a cost-effective choice.
Comparing Pressure-Treated Lumber to Alternatives
While pressure-treated wood is popular, it's worth considering other options for dock construction in Charleston.
Composite decking
Composite materials offer low maintenance but come at a higher initial cost. They may be less suited to structural components in saltwater environments.
Tropical hardwoods
Some Charleston dock builders use naturally durable hardwoods like ipe, which resist decay without chemical treatment but are more expensive.
Metal docks
Aluminum docks are becoming more common in Charleston, offering durability and low maintenance, but with a different aesthetic than traditional wood.
Future Trends in Pressure-Treated Lumber for Docks
The industry is constantly evolving, with new treatments and technologies emerging:
Micronized copper treatments
These newer preservatives offer improved performance and a more natural appearance, which may become more prevalent in Charleston dock construction.
Nanotechnology in wood preservation
Research into nanoparticle-based wood treatments could lead to even more durable and environmentally friendly options for future Charleston docks.
Expert Opinions on Pressure-Treated Lumber for Charleston Docks
Local marine contractors and wood scientists weigh in on the best practices for using pressure-treated lumber in Charleston's unique environment:
Insights from Charleston dock builders
Experienced local contractors share their preferred lumber grades and installation techniques for lasting results in Charleston waters.
Recommendations from wood preservation experts
Scientists from Clemson University's Wood Utilization + Design Institute offer insights on the latest advancements in pressure treatment technology.
Sourcing Pressure-Treated Lumber in Charleston
Where to find quality marine-grade lumber for your Charleston dock project:
Local suppliers
Charleston has several reputable lumber yards specializing in marine-grade pressure-treated wood.
What to look for when buying
Tips on inspecting pressure-treated lumber for quality and proper treatment before purchase.
DIY vs. Professional Installation
Considerations for Charleston homeowners deciding whether to tackle a dock project themselves or hire a pro:
Skills required
Building a dock requires carpentry skills, knowledge of marine construction, and familiarity with local regulations.
Tools and equipment
Specialized tools and heavy equipment are often necessary for dock construction in Charleston waters.
Safety considerations
Working over water presents unique safety challenges, especially in Charleston's tidal environments.
Making the Right Choice for Your Charleston Dock
Pressure-treated lumber remains a solid choice for dock construction in Charleston, offering a balance of durability, cost-effectiveness, and traditional aesthetics.
By understanding the specific needs of marine construction in the Lowcountry and following best practices for selection, installation, and maintenance, you can create a dock that will withstand Charleston's coastal conditions for years to come. For more information, you can visit our website or contact us.
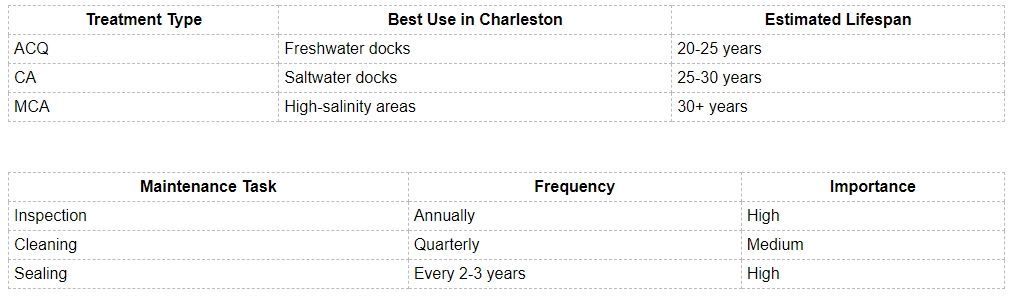
- Check for signs of decay or insect damage
- Tighten loose fasteners and replace as needed
- Clean with a pressure washer to remove salt and marine growth
- Apply a UV-resistant sealant to protect against sun damage
- Trim nearby vegetation to reduce moisture retention